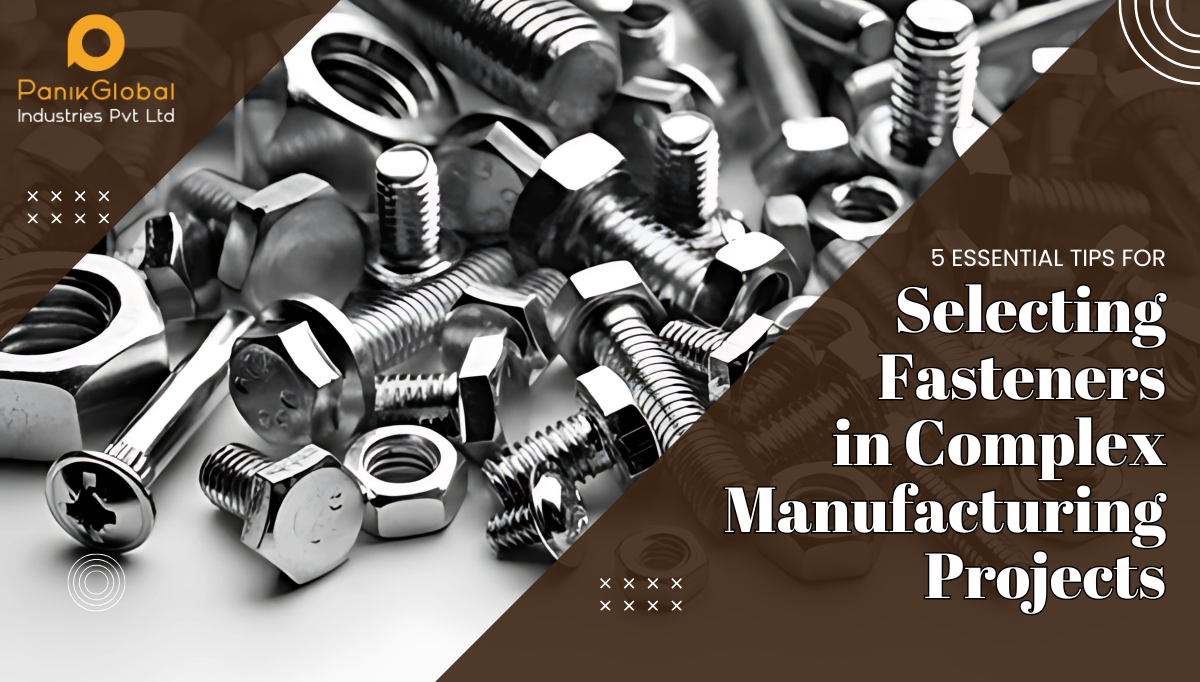
Table Of Contents
- Introduction
- Why Fastener Selection Matters in Complex Projects
- Tip 1: Understand the Application Environment (Where Will It Be Used?)
- Tip 2: Choose the Right Material: Strength, Durability & Cost
- Tip 3: Consider the Thread Type, Fit & Fastening Method
- Tip 4: Factor in Assembly, Maintenance, and Disassembly
- Tip 5: Ensure Compliance with Industry Standards & Certifications
- Bonus Tip: Always Work With an Expert Fastener Supplier
- Final Thoughts: A Small Decision With a Big Impact
- FAQs – Fastener Selection Simplified
Introduction
In any large or complex manufacturing project—whether it’s building airplanes, assembling cars, installing wind turbines, or manufacturing medical equipment—fasteners are the quiet champions that hold everything together.
But not all fasteners are the same.
Choosing the wrong type of bolt, screw, or nut can cause delays, safety risks, system failures, and even massive financial losses.
So how do you choose the right fasteners for demanding, multi-layered manufacturing environments?
Here are 5 in-depth, expert-backed tips that will help you avoid mistakes, improve efficiency, and boost the long-term success of your projects—from planning to production.
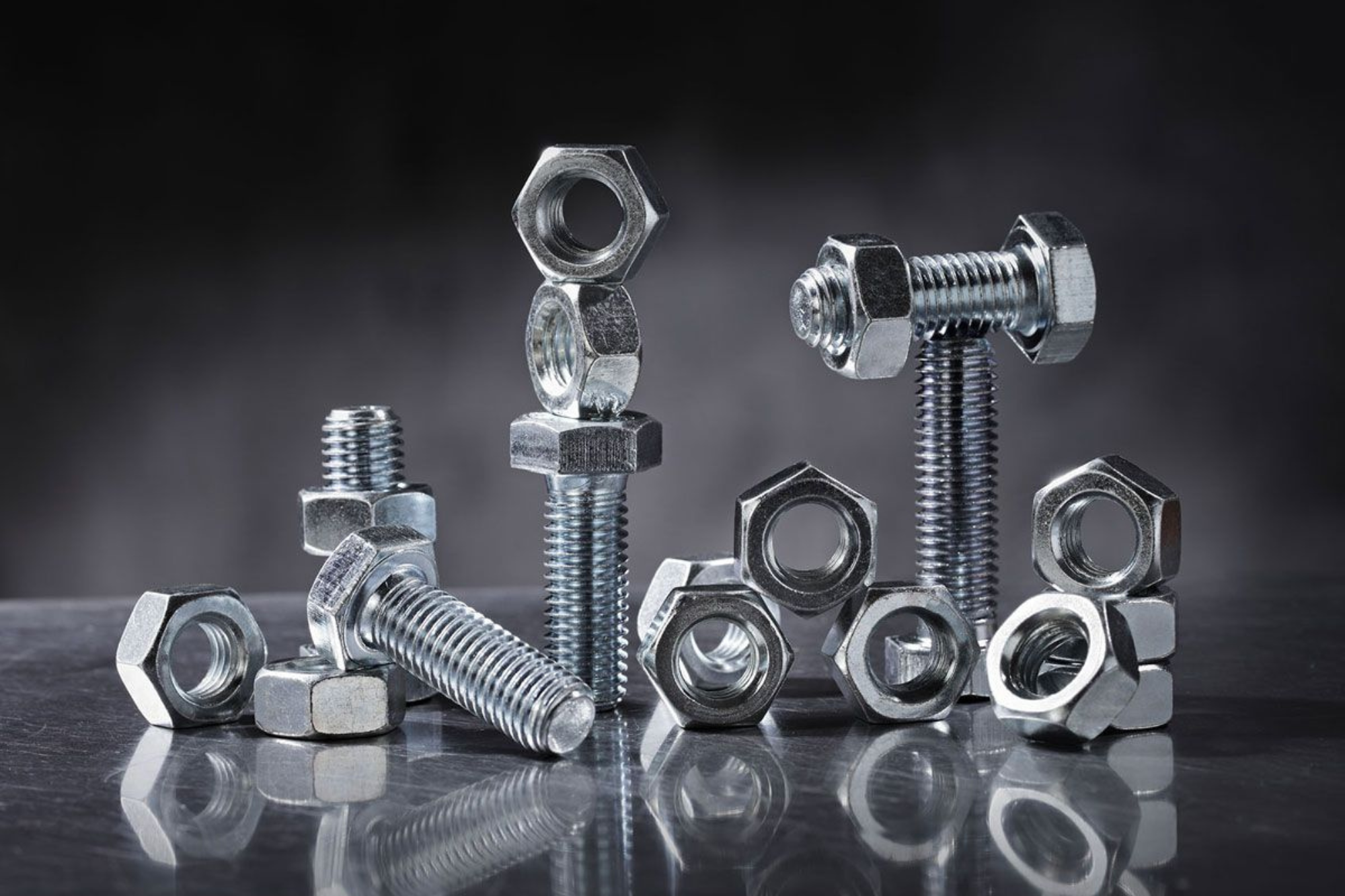
Why Fastener Selection Matters in Complex Projects
Before we jump into the tips, let’s understand the bigger picture.
In simple projects (like DIY furniture), fasteners are easy to pick. But in complex, high-value builds such as:
- Heavy machinery
- Aerospace assemblies
- Defense and automotive systems
- Renewable energy installations
- Advanced electronics
…the type, grade, finish, material, and torque of each fastener must be perfectly matched to the job. Even a minor mismatch can cause:
- Loose joints
- Rust or corrosion
- Poor vibration resistance
- Thermal failure
- Or total structural damage
And in industries like aviation or medical equipment, the consequences can be life-threatening.
So how do you avoid these issues?
Let’s explore the 5 essential tips.
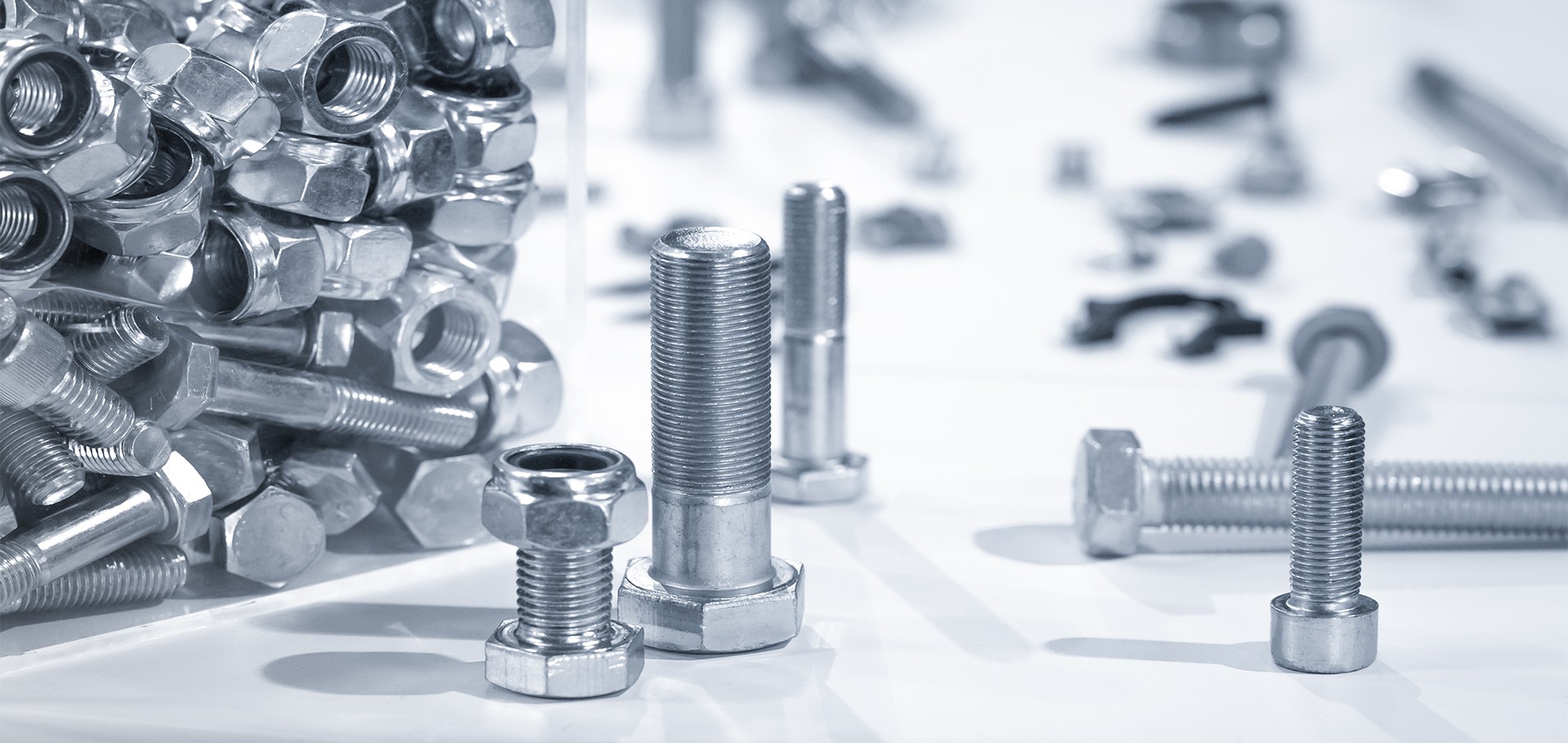
Tip 1: Understand the Application Environment (Where Will It Be Used?)
Every environment has its own challenges.
Fasteners are exposed to all kinds of real-world conditions: heat, humidity, chemicals, vibrations, pressure, and more. If you don’t match your fastener’s material and design to its working environment, you’re asking for trouble.
Ask These Questions:
- Will the fastener be used indoors or outdoors?
- Is the area coastal, humid, dusty, or exposed to chemicals?
- Will it experience heat, cold, pressure, or vibration?
- How accessible will it be for maintenance?
Match Fastener to Environment:
Environment | Best Fastener Type |
Coastal/Marine | Stainless steel 316 or titanium |
High Heat (Engines/Ovens) | Inconel or nickel alloys |
High Vibration (Motors) | Lock nuts, spring washers, nylocs |
Corrosive (Chemical plants) | PTFE-coated, galvanized, or brass |
Indoor (Low-stress) | Zinc-plated steel or carbon steel |
Real Example:
In Mumbai’s marine docks, stainless steel fasteners are a must. Regular steel bolts rust quickly due to salty air, causing frequent breakdowns in machinery and public structures.
Tip 2: Choose the Right Material: Strength, Durability & Cost
Fasteners come in many materials, and each serves a different purpose. Choosing the wrong material can make your project weaker or more expensive than it needs to be.
Let’s compare the most common materials:
Fastener Materials Breakdown
Material | Strength | Corrosion Resistance | Cost | Best For |
Carbon Steel | Moderate | Low | Low | General machinery & interiors |
Stainless Steel | High | High | Medium | Coastal, outdoor, wet environments |
Brass | Moderate | High | High | Electrical, aesthetic fittings |
Titanium | Very High | Excellent | Very High | Aerospace, medical, marine |
Aluminum | Low | Good | Medium | Lightweight electronics, small parts |
Nickel Alloys | Very High | Very High | High | High temperature/chemical environments |
Rule of Thumb:
- Use stainless steel or coated alloys when corrosion is a concern
- Use titanium or nickel alloys when strength-to-weight ratio is critical
- Avoid under-spec’d materials in high-risk projects—even if they’re cheaper
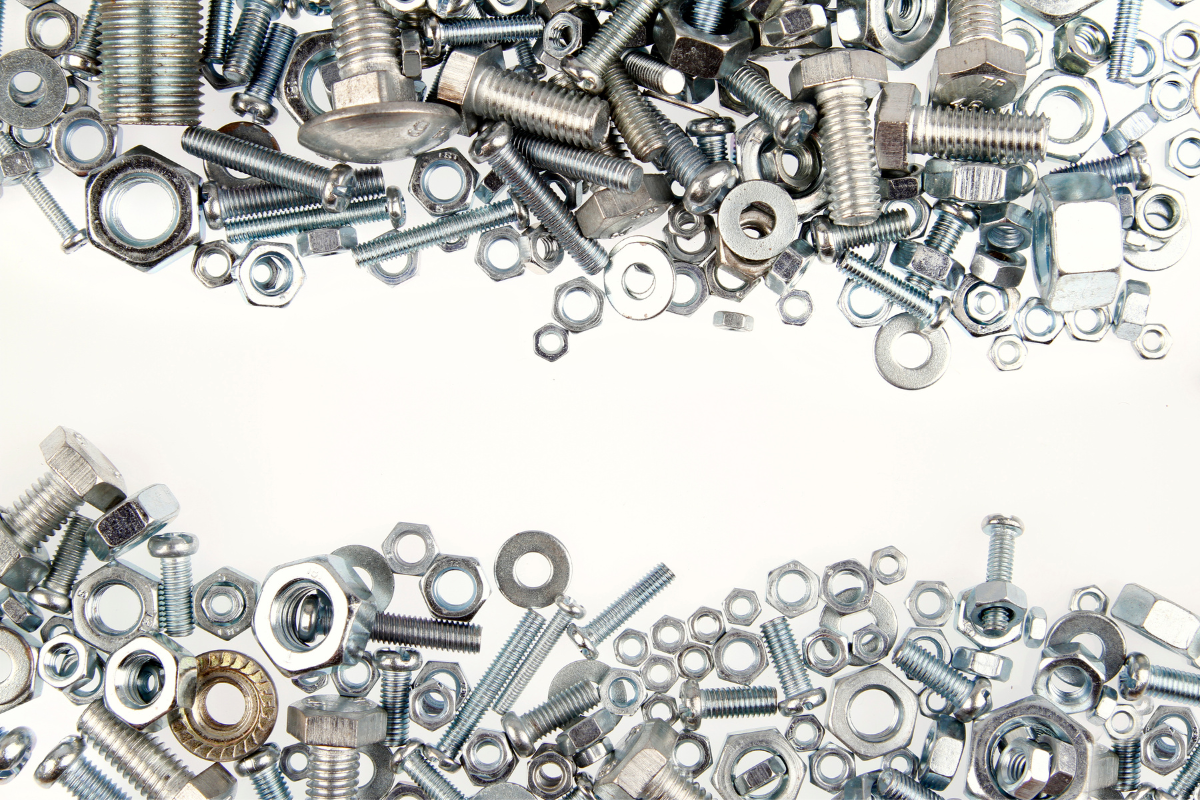
Tip 3: Consider the Thread Type, Fit & Fastening Method
When fasteners are installed into a system, they need to fit snugly—not too loose, not too tight. This depends on:
- Thread type (coarse vs fine)
- Thread standard (metric vs imperial)
- Tolerance class (how tight the fit is)
- Fastening method (torque, clamp load, preload)
Common Mistakes:
- Mixing up metric and imperial threads
- Over-tightening or under-tightening fasteners
- Using the wrong nut/bolt combo
- Ignoring vibration and thermal expansion
Pro Tip:
Always match threads based on manufacturer specifications. And use torque wrenches or automated tightening systems for precision.
In automotive plants in Pune, precision thread fitting is crucial for vehicle suspension systems—where any looseness can cause safety failures at high speeds.
Tip 4: Factor in Assembly, Maintenance, and Disassembly
In complex manufacturing, assembly and disassembly are common—whether it’s for testing, repairs, upgrades, or inspections. Your fasteners should make this easy—not harder.
Fasteners That Make Maintenance Easier:
- Hex bolts: Easy to tighten or loosen with a wrench
- Captive screws: Stay attached to a panel, avoiding drops
- Quick-release fasteners: Save time in frequent maintenance systems
- Tamper-proof fasteners: For secure or restricted access components
Reusable fasteners help reduce waste and speed up the maintenance cycle—great for sustainable manufacturing goals.
Example: In electronics hubs like Bangalore, modular PCBs and power systems are held with Phillips screws for easy upgrades or replacements—avoiding glue or solder where possible.
Tip 5: Ensure Compliance with Industry Standards & Certifications
Complex projects often serve high-risk industries: aerospace, energy, defense, infrastructure, medical devices. These sectors require strict compliance.
Using non-certified fasteners can cause:
- Legal liabilities
- Export rejection
- Safety audits failure
- Lost tenders or contracts
Key Standards to Check:
- ISO 898-1: Mechanical properties of bolts/screws
- ISO 3506: Stainless steel fasteners
- ASTM A193/A194: High temperature and pressure fasteners
- RoHS & REACH: For environmentally safe and non-toxic coatings
- DIN / BIS (India Standards): National manufacturing specs
Global Clients? Then this matters.
If you’re exporting to Europe or North America, certified fasteners are a must.
Panik Global supplies fully certified, RoHS-compliant, export-ready fasteners for advanced industries in India and abroad.
Bonus Tip: Always Work With an Expert Fastener Supplier
Fasteners seem simple, but they’re not. From torque requirements to anti-corrosion coatings, there are hundreds of small factors that can affect your build.
That’s why it’s smart to work with an experienced fastener supplier who:
- Provides engineering support
- Helps with material selection
- Offers technical documentation
- Has quality testing in place
- Can supply in bulk or custom sizes
That’s where Panik Global comes in.
We serve businesses across Mumbai, Delhi, Ahmedabad, Chennai, Bangalore, and beyond—with:
- Fast delivery
- Certified materials
- Industry-specific advice
- Long-lasting partnerships
Whether you’re building medical devices or metro lines, we help you choose the right fastener from day one.
Final Thoughts: A Small Decision With a Big Impact
Fasteners may be tiny, but in complex manufacturing, they carry massive responsibility.
Get it wrong? You’re stuck with costly rework and safety issues.
Get it right? Your system is stronger, more efficient, and built to last.
So, the next time you’re sourcing parts, remember—the right fastener isn’t just hardware. It’s your foundation.
Ready to Choose Fasteners Like a Pro?
Don’t leave it to guesswork.
Contact Panik Global today for:
- Expert consultation
- Certified fasteners
- Custom sourcing for your complex projects
Visit: www.panikglobal.com/contact
Let’s build better—bolt by bolt, project by project.
FAQs – Fastener Selection Simplified
Only if the conditions are the same. Always match the fastener to the specific stress, environment, and load of each project.
Ask for a Material Test Certificate (MTC) and check for standard markings (like ISO, ASTM) on the product.
Absolutely! Many are built for durability and reusability, which reduces maintenance and material waste.
Torque wrenches, thread gauges, and sometimes automated or robotic fastening systems for high-end manufacturing.